
“If you fail to plan, you are planning to fail.”
This quote by Benjamin Franklin hits home in a lot of areas of life. But it’s also very true when it comes to building a commercial real estate project.
When you’re building a condo or high-rise commercial building, there is a lot of planning that needs to happen. Otherwise, your project has a good chance of failing.

One of the most important plans is your budget. And you can’t budget without factoring in your elevator installation cost. More specifically, your elevator installation cost by project range.
An elevator is an absolute necessity for safety and convenience in your building. However, elevator repair costs can also have a high price tag.
Today we’ll be going over the various elevator repair costs by project range. By the time you’re done reading this article, you’ll have a much better idea of what you’re getting into when it comes to installing an elevator or repairing an elevator.
Best of all, you’ll be able to budget and set up a solid elevator installation plan. Let’s get going!

How To Install An Elevator
To understand the costs and where we can trim them, we first need to understand the overall elevator installation process. It can take time, but the process is simple. A trained professional can have your elevator up and running in 5 steps.
1. Set Your Columns
These columns become the framework for your elevator. The tricky part is that the design and measurement of the columns need to happen early on in the process. When taking on a big project like a high-rise or commercial building, many steel beams need to be erected.
To go back after the fact, and have to redo that installation to install an elevator, would slow down progress to a crawl. This is why it’s important to work with a professional.
An installer with the proper training will take care of all of the permits, planning, measurements, etc., to make sure your elevator goes in without a hitch. They should be installing the columns or elevator shaft first and foremost.
2. Installing the Carriage
The carriage is the technical term for the “box” that will carry all of your passengers. This needs to be carefully calculated to make sure every floor in your building can withstand the elevator’s weight.
If your installer follows the proper elevator safety protocols, this shouldn’t be an issue. Elevators are rated to handle the heavy load when installed the right way.
This is another time when you and your crew should be leaning on the experts in the field.
3. Raising the Drive Base
This is the machinery on top of the elevator that pulls it up and down the shaft. This is heavy equipment to pull the elevator at the appropriate speeds.
A crane, or other heavy machinery, is used to lift the drive base onto the top of the elevator. Once it’s in place, the installer bolts it down to the carriage, they then will finalize the process by welding it to the elevator supports.
4. Setting The Doors
The elevator doors must be mounted in place. If they aren’t, they can easily slide off-track and cause an elevator malfunction. They should be welded or bolted firmly into place.
5. Electrical Wiring
Now that the big tasks are done, it’s time to focus on what’s going to make this elevator run every day. The wiring workload will fall onto the installer. They will wire everything so that the elevator runs smoothly and easily with the push of a button.
Once these steps are complete, the installer will then double back to do a final check. An elevator incident can do a significant amount of damage. It can even be fatal.
That’s why it’s important to check thoroughly to ensure everything is done properly.
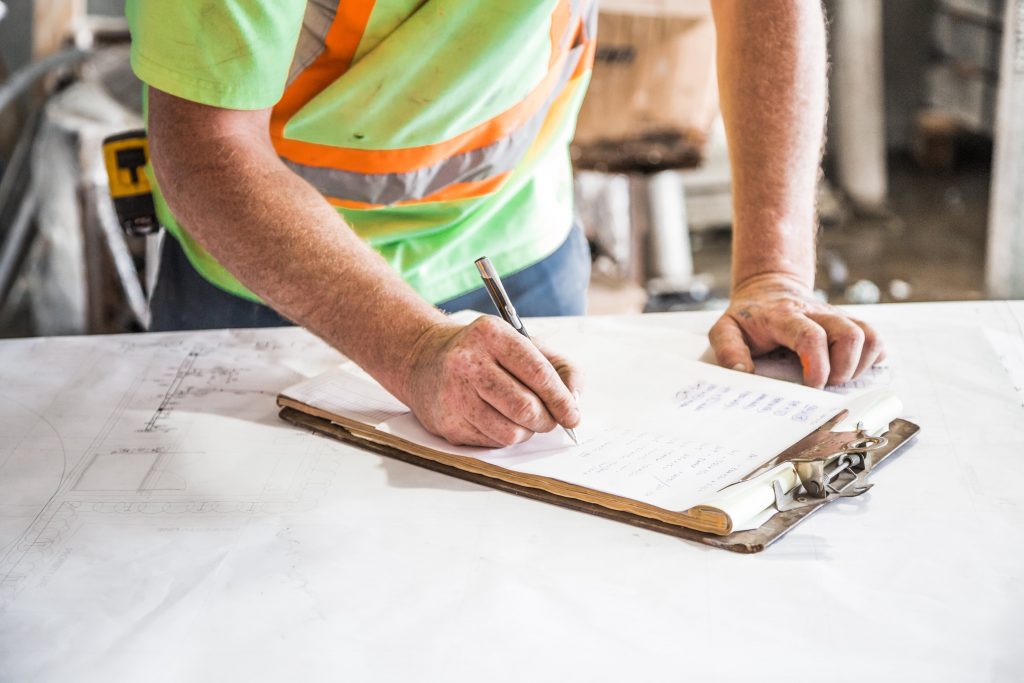
Things to Consider
Now that the elevator is up and running, there are some considerations to consider when researching repairs and maintenance.
One of the main things is the company you choose. Having the company that did the installation handle the maintenance and repairs makes the most sense.
They have an intricate knowledge of the project, and they’ll automatically be aware of any special considerations necessary for that particular elevator.
The typical lifespan of an elevator is twenty years. It’s helpful to know that fact to gauge the appropriate time for repairs.
If an installer is insisting on major repairs two to three years after installation, he may be dishonest. This isn’t always the case, but it should raise some suspicion. If this happens, it might be best to get a second opinion.
The lifespan also assumes regular care and maintenance. Like anything else, large or small, proper elevator care significantly prolongs the life of the elevator. It’s also a good idea to check with local laws and a local inspector to schedule regular inspections of the elevator and its parts.

Elevator Installation Cost Averages
So, how much will it cost to install an elevator? Well, that’s a great question. Of course, some things will depend on the size of the elevator.
The price will also be affected by how elaborate the elevator is. If the design of a building calls for marble floors in an elevator, that will be much more costly than an elevator with carpet flooring.
All of that being said, however, there are some standard elevator installation costs.
Overall, a commercial elevator project can start anywhere from $50,0000 to $60,000 and go up from there.

Elevator Installation Cost by Project Range
That base price is the standard for a two-story building. Depending on how many floors the building has, the price can go up (ha! no pun intended) from there.
There are several different factors that come into play once you start to design and install bigger elevators.
The first would be the actual framework. Larger elevators that travel higher distances require more steel and aluminum to construct. They also weigh more and will probably be holding more weight during operation.
All of this means more money for raw materials and also more money for safety engineering. As mentioned earlier, elevator safety is no laughing matter.
Installers and inspectors take this stuff very seriously. As such, large elevator projects require a lot of safety precautions. And they’re a lot more expensive safety precautions.
The next factor would be the finishes. These can be some of the highest ticket items in an elevator install project. High-rise luxury apartments and condos are quickly becoming the wave of the future.
Elevator designs and trim need to match the aesthetics of these state-of-the-art buildings. The materials used for finishes can also tie into the safety of the elevator.
If an architect or designer wishes to use high-end tiles or other fixtures in an elevator carriage, that can drastically add to the weight of the overall elevator.
It’s important that the elevator installer, architect, and designer all work as a team to make sure the elevator installs and operates as smoothly as possible.
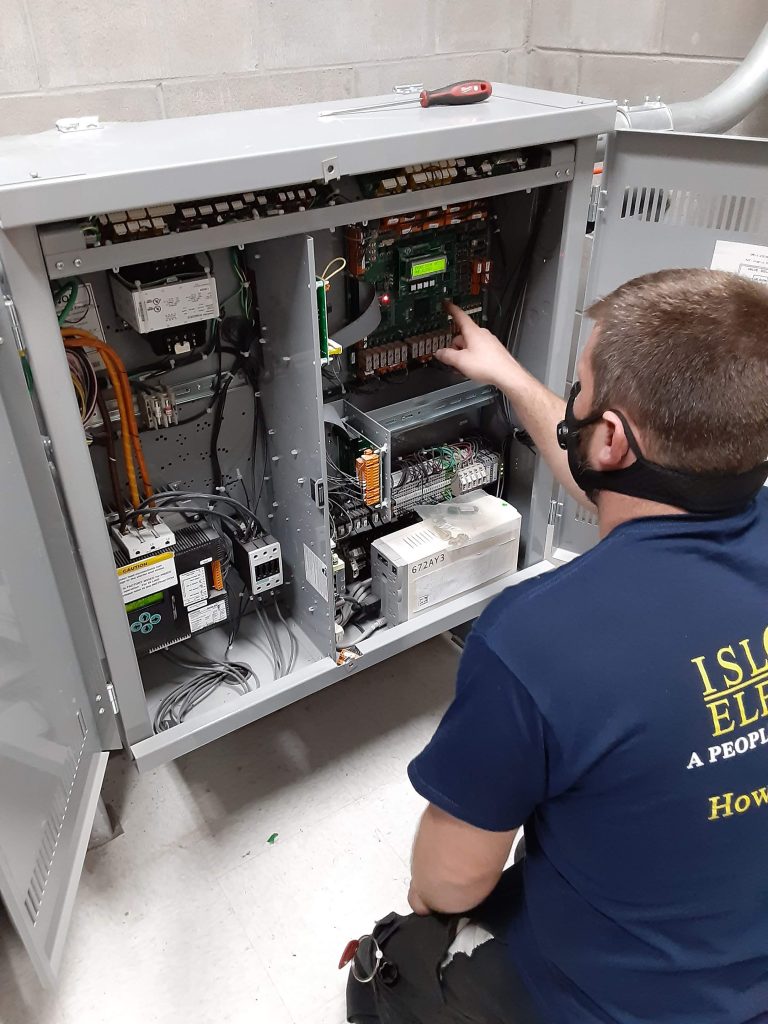
Machine-Room vs. MRLs
The two major types of elevators to install in commercial buildings are machine-room elevators vs machine-roomless elevator. MRL stands for Machine-roomless Lifts.
Both types of elevators have distinct advantages and disadvantages. MRLs take up significantly less room in a building. They also consume less power while in operation.
MRLs are a great option for a freight elevator. They can accommodate heavy loads. They also require less on-site service time and cut down on the use of hydraulic oil.
There are some downsides to MRLs as well. One of the most significant is standby power. The MRL will be consuming more energy than a traditional elevator when it’s not in use. They are also more expensive and take longer to install than their machine-room counterparts. They also come with a higher elevator replacement cost.
Machine-room elevators are a reliable option, but, like the name states, they require a machine room. The size of the typical machine room for a commercial elevator runs about 25 square feet.
In certain types of elevators, though, this machine room can be strategically positioned on top of the elevator cab. This can save a commercial developer valuable square footage that is useful for another purpose.
Really, it’s a personal choice when it comes to which type to use. The downside of having a machine room can be easily offset by installing the machine room above the cab.
Therefore, it would appear that a machine-room lift would have more avoidable disadvantages than an MRL.

The Sky Is The Limit
Elevator installation cost by project range is something every developer, architect, and engineer needs to consider when taking on a new commercial project. Since it’s a central part of any high-rise building, it needs to be thought out and planned carefully in order to be a success.
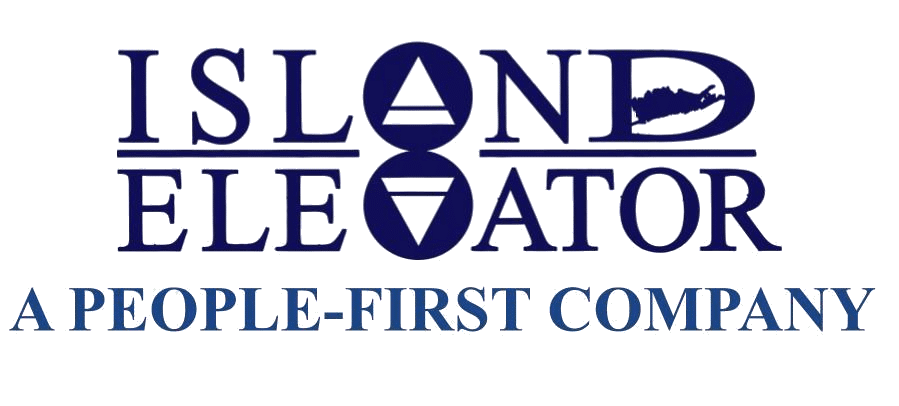
Island Elevator is here to help you understand all facets of your Elevator Repair, Maintenance, & Modernization costs in the new year. Our team is here to help ensure your home and business vertical transportation equipment receive the regularly scheduled maintenance necessary to help you avoid a major catastrophe, reduce the possibility of a costly repair, and ensure the safety of your passengers, tenants, and family.