If you manage a hotel, then you know that having a functional elevator is critical. After all, your guests rely on being able to move around the hotel with ease.
When something goes wrong with the elevator, it can cause a major disruption. That’s why it’s so important to have a reliable elevator parts specialist that you can turn to when you need help. Here are three reasons why using an elevator parts specialist is a good idea:

1. They have experience working with all types of elevators.
When it comes to elevator maintenance, too often managers think they can cut corners by only servicing the major components. However, failing to properly maintain all parts of the system can lead to serious consequences. For example, one small part that is often neglected is the door operator. This crucial component ensures that the doors open and close smoothly and evenly. If the door operator isn’t functioning properly, it could cause the doors to open partially, which could result in an injury if someone gets caught in between them.

2. They can help you troubleshoot issues over the phone.
If you need help finding the right elevator parts, then working with an elevator parts specialist is a good idea. They will be able to help you find the right parts for your specific elevator and can even troubleshoot issues over the phone. Plus, they usually have a wide selection of parts in stock, which means you won’t have to wait weeks for the part to arrive.
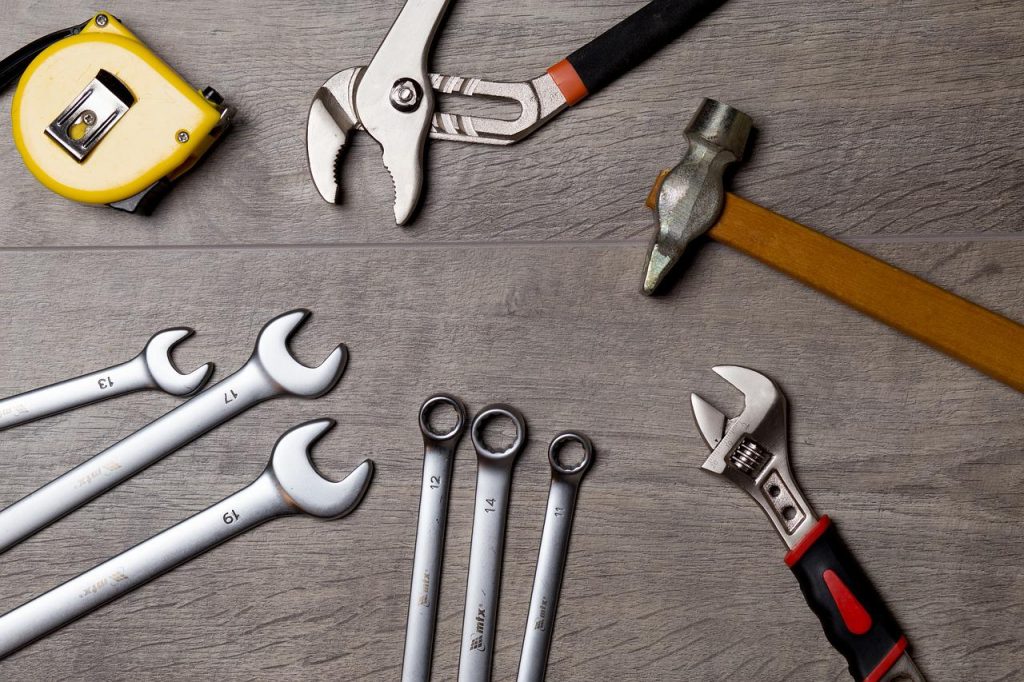
3. They usually have a wide selection of parts in stock.
If you need help finding the right elevator parts, then working with an elevator parts specialist is a good idea. They will be able to help you find the right parts for your specific elevator and can even troubleshoot issues over the phone. Plus, they usually have a wide selection of parts in stock, which means you won’t have to wait weeks for the part to arrive.

Elevator Maintenance: Why You Can’t Skimp on the Small Stuff
Whether you manage a hotel, office building, or residential complex, you know that having a functional elevator is crucial. But what you may not realize is that all the small parts that make up your elevator system play a big role in keeping it running smoothly. In this blog post, we’ll break down why it’s important to keep up with maintenance on all elevator parts, no matter how small they may seem.
Another small part that should never be overlooked is the safety edge. The safety edge is a pressure-sensitive strip typically found along the bottom of the elevator door. Its purpose is to detect when something is obstructing the door from closing, which will then cause the doors to reopen. If the safety edge isn’t working correctly, it could allow the doors to close despite an obstruction, resulting in serious injury or even death.
In short, there’s no such thing as a “minor” maintenance issue when it comes to elevators. Neglecting any part of the system – no matter how small – can put your riders at risk.

Why You Should Use The Right Elevator Parts Supplier
The next time you’re tempted to skip out on servicing some of the smaller parts of your elevator system, remember that even tiny maintenance issues can have major consequences. By staying on top of all aspects of your elevator’s upkeep, you can help ensure a safe and smooth ride for everyone who uses it.
If you manage a hotel, you know that one of the most important aspects of keeping your guests happy is making sure that the elevator is working properly at all times. After all, no one wants to be stuck in a hotel elevator! That’s why it’s so important to use a reputable supplier for all of your elevator parts needs. Here’s why:

1. Quality Parts Matter
The last thing you want is for your guests to be stuck in an elevator because of a broken part. When you use a reputable supplier, you can rest assured that you’re getting high-quality parts that will stand up to wear and tear. Cheap, imitation parts may save you a few dollars upfront, but they’ll end up costing you more in the long run when they need to be replaced more often.
2. Better Customer Service
When something goes wrong with your elevator, you need to be able to rely on your parts supplier for help. A good supplier will have knowledgeable customer service representatives who can help diagnose the problem and find the right solution. With a less reputable supplier, you may have to wait days or even weeks for someone to get back to you—and in the meantime, your guests will be none too pleased.
3. Increased Safety
On top of everything else, using high-quality elevator parts from a reputable supplier can actually help increase safety for your guests. That’s because well-made parts are less likely to fail unexpectedly, which could put your guests at risk. inferior parts, on the other hand, are more likely to break down without warning—and that could lead to dangerous situations.
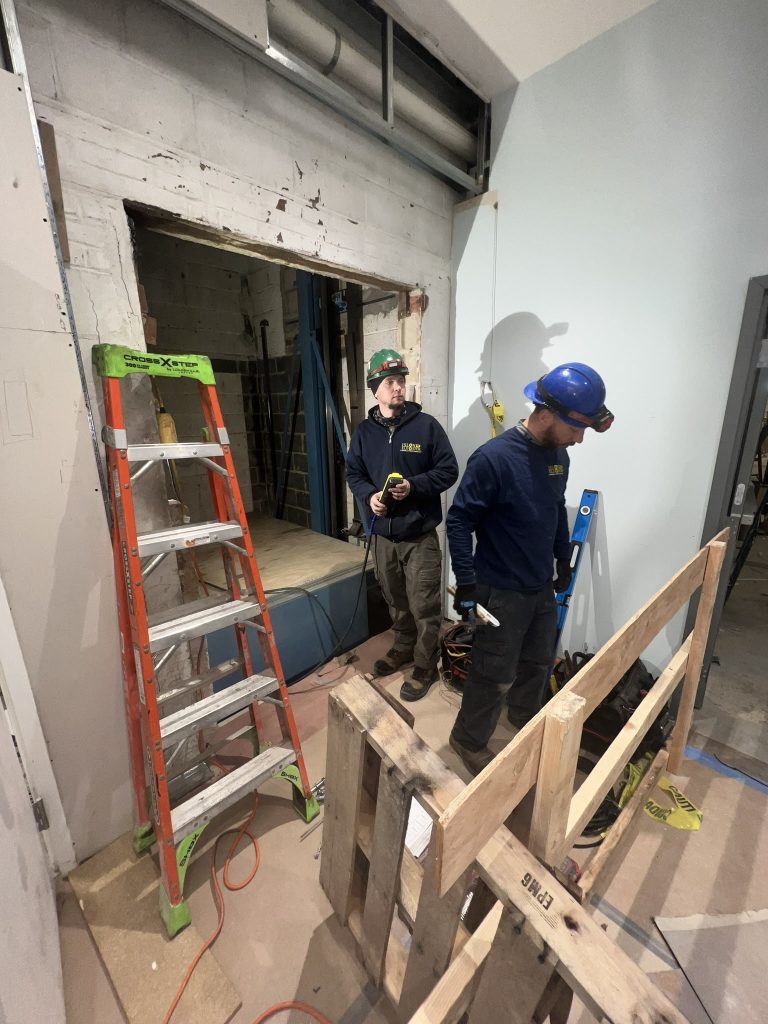
Conclusion:
As you can see, there are many good reasons why you should use a reputable supplier for all of your elevator parts needs. From increased safety to better customer service, choosing a quality supplier will help ensure that your hotel runs smoothly—and that your guests are always happy.
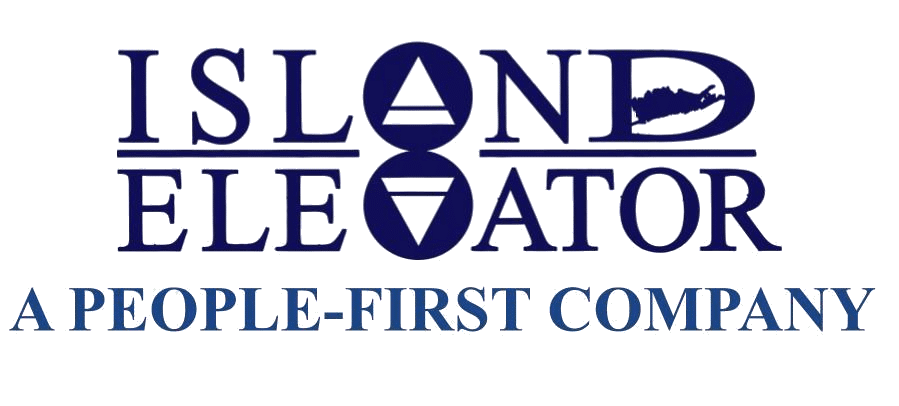
Island Elevator is Ready to Help
Island Elevator is here to help you understand all facets of your Elevator Repair, Maintenance, & Modernization costs in the new year. Our team is here to help ensure your home and business vertical transportation equipment receive the regularly scheduled maintenance necessary to help you avoid a major catastrophe, reduce the possibility of a costly repair, and ensure the safety of your passengers, tenants, and family.